Технологии наплавки
При осуществлении того или иного процесса наплавки происходит оплавление поверхности металла - основы, расплавление присадочного материала, соединение их и кристаллизация образовавшейся смеси. Соотношение долей основного и присадочного металлов в наплавленном слое определяет его состав, микроструктуру и свойства. При восстановительной наплавке нелегированным металлом доля основного металла не оказывает существенного влияния на свойства наплавленного слоя. Напротив, при упрочняющей наплавке легированным металлом увеличение доли основного металла приводит к ухудшению свойств наплавленного слоя.
Ручную электродуговую наплавку выполняют на постоянном и переменном токе штучными неплавящимися или плавящимися электродами. В качестве неплавящегося электрода чаще всего используют графитовые (угольные) стержни. На наплавляемую поверхность наносят слой наплавочной смеси или пасты соответствующего состава и расплавляют теплом дуги. Толщина наплавленного слоя -1-3 мм. Угольным электродом по слою смеси чаще всего наплавляют плоские поверхности. Более распространена наплавка плавящимися покрытыми электродами. Достоинства способа: простота и маневренность; недостатки: низкая производительность (1-3 кг/ч), тяжелые условия труда, снижение усталостной прочности наплавленных деталей.
Достоинствами механизированной наплавки являются: непрерывность процесса, достигаемая в результате использования электродной проволоки или ленты в виде больших мотков; подвод тока к электроду на минимальном расстоянии от дуги, позволяющий применять токи большой силы без перегрева электрода.
Из всех способов механизированной наплавки наибольшее распространение получила наплавка под флюсом. Схема этого способа показана на рис.8. Электродная проволока 1 непрерывно с постоянной скоростью подается в дуговой промежуток. Подвод тока к проволоке осуществляется в непосредственной близости от дуги при помощи втулки 2. В дуге 3 проволока плавится.
Капли металла, пройдя дуговой промежуток, смешиваются с расплавленным металлом изделия 4 и образуют сварочную ванночку 5. После кристалли зации получается наплавленный валик 6, покрытый шлаковой коркой 7 и нерасплавившимся флюсом 8. Избыток флюса ссыпается, а остывшая шлаковая корка удаляется. Формируется однородный наплавленный металл без пор и раковин. Производительность процесса одноэлектродной наплавки под слоем флюса невелика.
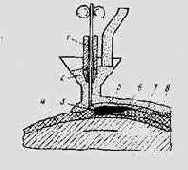
Рис.8
Поэтому наряду с одноэлектродной наплавкой применяют и другие разновидности этого способа: наплавку электродной лентой, многоэлектродную и многодуговую наплавку, наплавку с поперечным колебанием электрода (рис.9,а,б,в,г)
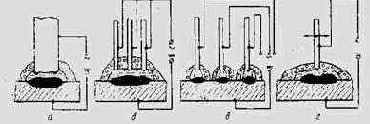
Рис.9
При наплавке электродной лентой (рис.9,а) достигаются малая глубина проплавления основного металла и возможность наплавить за один проход валик шириной до 100 мм. При многоэлектродной наплавке (рис. 9,б) в зону дуги одновременно подаются несколько электродов, подключенных к одному полюсу источника сварочного тока. Дуга периодически перемещается с одного электрода на другой; при этом образуется общая сварочная ванна, формируется широкий валик. При многодуговой наплавке (рис. 9, в) применяется несколько наплавочных аппаратов или один аппарат с изолированными друг от друга несколькими электродами, каждый электрод питается от отдельного источника тока.
При наплавке деталей малого диаметра, глубоких внутренних поверхностей и ряда высоколегированных сплавов затруднено удаление шлаковой корки. Этого недостатка лишена механизированная наплавка открытой дугой и наплавка в защитных газах. При наплавке открытой дугой в качестве электрода используется порошковая проволока. Для защиты металла от кислорода и азота воздуха в ее сердечник вводят, кроме легирующих элементов, газо- и шлакообразующие компоненты и раскислители (при наплавке крупных деталей используют не порошковую проволоку, а ленту). Иногда используют голую легированную проволоку, содержащую в небольших количествах РЗМ
Наплавку в защитных газах чаще выполняют плавящимся электродом. В каче стве защитных газов используют углекислый газ, аргон, азот.
Вибродуговая наплавка.
Схема процесса показана на рис.10. Характерной особенностью способа является применение вибрирующего плавящегося электрода. Электрод в виде голой проволоки подается в дугу специальным аппаратом, который обеспечивает вибрацию электрода вдоль его оси. В результате процесс состоит из циклов, в каждом из которых происходят: 1) замыкание электрода с наплавляемой поверхностью; 2) размыкание и образование дуги; 3) подача электрода к изделию до замыкания. Длительность циклов определяется частотой вибрации электрода. Частота вибрации электродов обычно составляет 30 - 100 пер/с; амплитуда -0,75 - 1,0 диаметра электрода. Производительность вибродуговой наплавки мала (0,5 - 3,0 кг/ч), поэтому восстанавливать этим способом крупные детали с большим износом не рекомендуется. На рис. 10: 1- кассета с электродной проволокой;2 – механизм подачи проволоки; 3 - электромагнит вибратора; 4 - вибрирующий рычаг; 5 - опорный узел; 6 - хоботок; 7 –изделие.
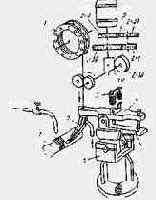
Рис.10
Электрошлаковая наплавка (ЭШН)
Схема процесса показана на рис. 11.
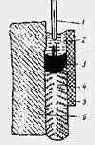
Рис.11
В пространстве, образованном наплавляемой поверхностью 6 и формирующим устройством 5, создается ванна расплавленного флюса-шлака 2, в которую непрерывно подается металлический электрод 1. Ток, проходя между электродом и наплавляемым изделием, нагревает расплавленный шлак и поддерживает высокую температуру и электропроводность. Шлак расплавляет электрод и оплавляет поверхность изделия. Ниже шлаковой ванны образуется металлическая ванна 3, которая, затвердевая, дает слой 4, прочно сплавленный с металлом изделия. Процесс наплавки начинают на графитовых, медных или стальных подкладках. Формирующее устройство в виде охлаждаемого водой медного ползуна медленно перемещается вверх с помощью специального механизма.
При электрошлаковой наплавке в качестве электродов используют проволоку, литые стержни и пластины, трубы, в качестве шлака - флюс АН-25. Благодаря применению больших токов (несколько тысяч ампер) достигают очень высокой производительности - до 150 кг наплавленного металла в час. ЭШН плоских поверхностей может производиться при вертикальном, нижнем и наклонном положениях наплавляемой поверхности.
Для торцовой наплавки деталей сложной формы используется прием стыкошлаковой наплавки (рис.12).
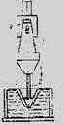
Рис.12
Процесс начинается наведением шлаковой ванны на дне водоохлаждаемой формы. Электродом служит хвостовик детали 1 с приваренной пластиной или прутком из легированного металла 2, которые расплавляются в первую очередь. В момент погружения хвостовика 1 в шлак происходит его разогрев, а затем он погружается в металлическую ванну. Таким образом успешно восстанавливают зубья экскаваторов, сверла и метчики большого диаметра и т.п.
Плазменную наплавку применяют в тех случаях, когда необходимо наплавить слой толщиной от 0,5 до 5,0 мм при строго регламентированной доле основного металла. Применяют несколько разновидностей плазменной наплавки. Присадочный материал нужного состава подают в плазменную дугу или выделенную плазменную струю в виде проволоки, ленты спрессованных металлокерамических колец, пластин, пасты или порошка. На рис.13 показана схема плазменной наплавки с токоведущей присадочной проволокой.
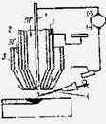
Рис.13
Источником тепла для расплавления присадочной проволоки является двухдуговой разряд. Одна дуга (маломощная) горит между вольфрамовым электродом 1 и соплом 2, вторая (основная) - между вольфрамовым электродом и проволокой 4. Через сопло 3 подается защитный газ. Основной металл разогревается теплом перегретого расплавленного металла проволоки и факелом плазменной струи. По этой схеме наплавляются: бронзы, латуни, нержавеющие стали и т.п.
На рис. 14 показана схема плазменно-порошковой наплавки.
Порошок нужного состава вдувают в дугу через специальные каналы в горелке. Во внутреннем рабочем сопле 2 формируется плазменная струя, по соплу 3 подается присадочный порошок, а по соплу 4 - защитный газ. Источник 5 служит для зажигания дуги между электродом 1 и соплом 2; в плазменной струе этой дуги плавится порошок. Источник 6 формирует плазменную дугу прямого действия, которая оплавляет поверхность изделия и является дополнительным источником тепла для плавления присадочного порошка. Производительность указанных способов невелика (0,5-10 кг наплавленного металла в час). Более высокой производительностью (до 30 кг/час) обладает плазменная наплавка с подачей в ванну двух плавящихся электродов.
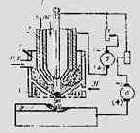
Рис.14
При индукционной наплавке в качестве источника нагрева используются токи высокой частоты. Нагрев осуществляется с помощью индуктора, присоединенного к машинному или ламповому генератору ТВЧ. Практическое применение нашли два способа индукционной наплавки: 1) с использованием твердого присадочного материала, наносимого на наплавляемую поверхность в виде порошка, пасты или прессованных брикетов; 2) с использованием жидкого присадочного материала, расплавляемого в отдельной индукционной печи и определенными порциями подающегося на разогретую поверхность наплавляемой детали. Наплавку твердым присадочным материалом применяют для повышения износостойкости бил и молотков дробилок, лап культиваторов, лемехов плугов (рис.15). На рисунке. 1- деталь, 2 - смесь порошков сплава и флюса, 3 - индуктор. В качестве присадочного материала используют порошок сплава сормайт 1, а также композиции сормайт - релит, сормайт - феррохром. Применяют также индукционную наплавку клапанов двигателей внутреннего сгорания. Присадочный материал в виде литых колец из сплава ВЗК или НХ15С2Р2 укладывают в предварительно проточенную канавку на тарелке клапана, а затем расплавляют с помощью специальных индукторов.

Рис.15
Наплавку жидким присадочным металлом в свою очередь подразделяют на: 1) наплавку заливкой жидкого присадочного сплава; 2) наплавку намораживанием. При наплавке заливкой жидкого металла толщина наплавляемого слоя должна быть более 5 мм, а соотношение массы наплавленного металла к массе металла - основы достигает 30 %. Преимущества этого метода: а) нет необходимости в изготовлении и применении сварочной проволоки, ленты и т.д.; б) возможность наплавки "ненаплавляемых" пар металлов (чугун на чугун, чугун на сталь и др.). При наплавке заливкой жидкого присадочного сплава (рис. 16) наплавляемую деталь 1, поверхность которой покрыта слоем защитного флюса 2, нагревают с помощью индуктора 4 токами высокой частоты и помещают в литейную форму 3; расплавленный металл заливают в пространство между наплавляемой поверхностью и внутренней поверхностью формы. После затвердевания расплав формирует наплавленный слой, имеющий надежное сцепление с металлом - основой.
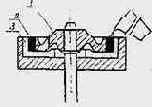
Рис.16
Разновидностью описанного способа является "дуплекс - заливка". При ее осуществлении по наплавляемой поверхности детали, помешенной в литейную форму, перепускают большое количество расплава. В результате этого поверхность разогревается. Последняя порция расплава кристаллизуется на ней и формирует наплавленный слой. Излишки жидкого металла сливают в стоящую рядом с первой литейную форму.
Наплавкой намораживанием (рис.17) компенсируют износы от 0,5 до 3 мм. При ее осуществлении наплавляемую деталь 1 нагревают в тигле с расплавленным шлаком 2, а затем быстро переносят в тигель с расплавленным присадочным металлом 3 и выдерживают в течение 0,5 - 1,5 секунд. За это время на наплавляемой поверхности кристаллизуется ("намораживается") слой указанной толщины.
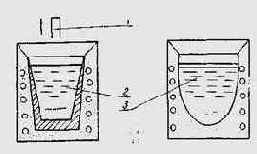
Рис.17
Для надежного сплавления присадочного металла с металлом - основой последний должен быть нагрет до температуры, большей tн:

где tp , tм.о- температура расплава и металла - основы, соответственно; b2, b1 -теплоаккумулирующие способности жидкого и твердого металлов, соответственно.