Построение расчетной схемы и коррекционный
При проектировании круглого фасонного резца с точкой по центру для вычерчивания расчетной схемы выполняются следующие построения (рис.5.1):
1. Из точки О1, представляющей на схеме ось вращения детали, проводят ряд концентрических окружностей радиусами, равными радиусам узловых точек профиля детали (r1, r2, r3,...rn). Пересечение окружности минимального радиуса (радиуса r1) с горизонтальной прямой определяет точку T1 профиля детали.
2. На расстоянии h0, равном

от горизонтальной прямой, проходящей через центр детали О1, проводят прямую, параллельную оси детали, и из точки T1 делают засечку на этой прямой радиусом R1. Таким образом определяют положение центра круглого резца (точки О0 расчетной схемы).
3. Из точки T1 под углом g1 к горизонтальной прямой проводят прямую, представляющую на схеме переднюю поверхность резца, которая для фасонного резца с базовой точкой по центру является плоскостью. Все остальные узловые точки режущей кромки резца определяются как результат пересечения следа плоскости передней поверхности резца с окружностями соответствующих радиусов детали (точки T2, T3,...Tn).
4. Соединив точки T2, T3,...Tn с центром резца О0 и, опустив из точки О0 перпендикуляр на плоскость передней грани до пересечения с ней в точке K0, получим ряд прямоугольных треугольников, имеющих общий прямой угол в точке K0, общий катет H0, равный

и гипотенузы, равные искомым радиусам узловых точек резца, то есть радиусам R2, R3,...Rn.
5. Опустив из центра детали (точки О1) перпендикуляр на след плоскости передней грани резца, получим точку K. Соединив отрезками центр детали О1 с точками T2, T3,...Tn, получим группу прямоугольных треугольников, имеющих общий прямой угол в точке K и общий катет h, равный

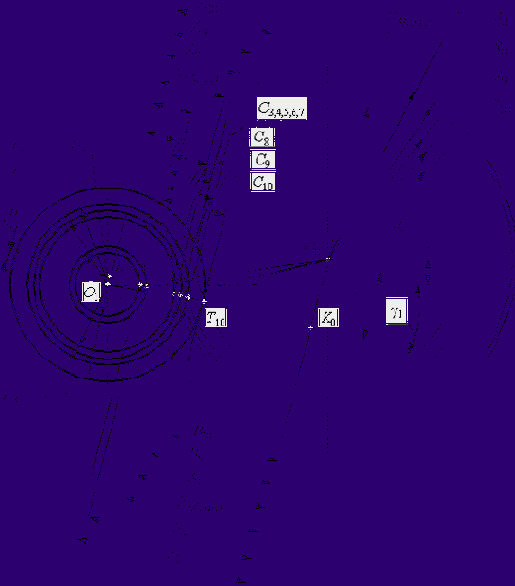
Рис. 5.1. Расчетная схема коррекции профиля круглого фасонного резца
6. Для удобства дальнейших вычислений обозначим расстояния от точки K до каждой точки профиля резца символом А с соответствующим индексом (А1, А2,...Аn), а расстояния от точки T1 профиля до остальных узловых точек – символом C с индексом (C2, C3,...
Сущность определения профиля призматического фасонного резца с точкой по центру детали сводится к определению расстояний Pi от узловых точек профиля резца до образующей задней поверхности, проходящей через точку, расположенную по центру детали, и определению осевых размеров li. Построение расчетной схемы призматического фасонного резца иллюстрируется рис. 5.2 и сводится к выполнению следующих процедур:
1. Из точки О1, представляющей на схеме ось вращения детали, проводят ряд концентрических окружностей радиусами, равными радиусам узловых точек профиля детали (r1, r2, r3,...rn). Пересечение окружности минимального радиуса (радиуса r1) с горизонтальной прямой определяет точку T1 профиля детали.
2. Из точки T1 под углом g1 к горизонтальной прямой проводят прямую, представляющую на схеме переднюю поверхность резца, которая для фасонного резца с базовой точкой по центру является плоскостью. Все остальные узловые точки режущей кромки резца определяются как результат пересечения следа плоскости передней поверхности резца с окружностями соответствующих радиусов детали (точки T2, T3,...Tn).
3. Для образования заднего угла a1 тело призматического резца при его установке наклоняется так, что образующая задней поверхности, проходящая через точку T1, образует необходимый по величине задний угол a1 с плоскостью резания в той же точке профиля. Таким образом, для представления задней поверхности резца на схеме, через точку T1 необходимо провести прямую, составляющую с вертикалью угол a1. Тогда образующие задней поверхности, проходящие через точки T2, T3,...Tn будут представлены на схеме прямыми линиями, параллельными к образующей задней поверхности, проходящей через точку T1.
4. Опустив из центра детали (точки О1) перпендикуляр на след плоскости передней грани резца, получим точку K. Соединив отрезками центр детали О1 с точками T2, T3,...Tn, получим группу прямоугольных треугольников, имеющих общий прямой угол в точке K и общий катет h, равный

Коррекционный расчет профиля призматического фасонного резца с базовой линией по центру детали (как и круглого) проводится последовательно по отдельным участкам профиля детали (участкам I, II, III и т.д.). Кроме того, процедуры построения расчетных схем на первых этапах практически полностью совпадают с аналогичными процедурами для круглого фасонного резца. Вследствие этого, при изложении процедур проектирования призматического резца расчетные схемы не дублируются, а даются ссылки на соответствующие рисунки, приведенные в разделе 5.3. Все схемы соответствуют случаю проектирования фасонного резца для обработки детали, представленной на рис. 4.3 (см. С.33).
Построение расчетной схемы и проведение аналитического расчета призматического фасонного резца с базовой линией по центру изделия сводится к следующей последовательности шагов:
1. Построение расчетной схемы резца начинается с рассмотрения участка профиля инструмента, обрабатывающего конический элемент детали (участка I). На первом выполняются следующие построения (см. рис. 5.8):
1.1. Из точки О1, представляющей на схеме ось вращения детали, проводят концентрические окружности радиусами r1 и r2 (r1 и r2 ? радиусы граничных узловых точек T1 и T2). Точки T1 и T2 - граничные узловые профиля детали на участке I, соответствующем коническому элементу изделия. Так как точки T1 и T2 принадлежат базовой линии, на схеме они будут представлены точками, которые находятся на пересечении горизонтальной прямой, проходящей через центр детали О1 с окружностями, имеющими радиусы r1 и r2. Как можно заменить, вследствие этого весь участок профиля инструмента T1?T2 находится в одной плоскости с осью изделия.
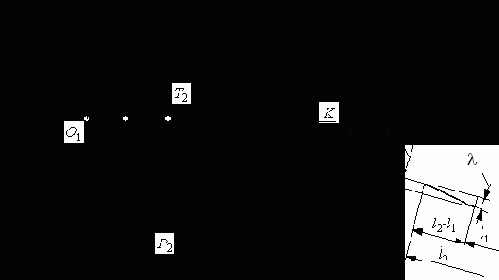
Рис. 5.8. Схема для определения положения центра O0 и угла l круглого фасонного резца с базовой линией по центру изделия
1.2. Для образования заднего угла a1 тело призматического резца наклоняется таким образом, чтобы образующая задней поверхности, проходящая через точку T1, образовывала с поверхностью резания угол необходимой величины.
Расчет профиля фасонного резца с базовой линией по центру детали (как круглого, так и призматического) несколько сложнее, чем расчет резцов с базовой точкой. Вследствие этого, целесообразно строить расчетную схему и проводить коррекционный расчет по отдельным участкам профиля (участкам I, II, III и т.д.).
Изложение процедур построения расчетной схемы иллюстрируется схемами, соответствующими детали, представленной на рис.4.3 (см. С.33). Построение расчетной схемы круглого фасонного резца с базовой линией по центру изделия сводится к следующей последовательности шагов:
1. Построение расчетной схемы резца начинается с рассмотрения участка профиля инструмента, обрабатывающего конический элемент детали (участка I). На первом шаге определяется положение центра инструмента (точки O0). Для этого выполняются следующие построения (см. рис. 5.3):
1.1. Из точки О1, представляющей на схеме ось вращения детали, проводят концентрические окружности радиусами r1 и r2 (r1 и r2 ? радиусы граничных узловых точек T1 и T2). Точки T1 и T2 - граничные узловые профиля детали на участке I, соответствующем коническому элементу изделия. Так как точки T1 и T2 принадлежат базовой линии, на схеме они будут представлены точками, которые находятся на пересечении горизонтальной прямой, проходящей через центр детали О1 с окружностями, имеющими радиусы r1 и r2. Как можно заменить, вследствие этого весь участок профиля инструмента T1?T2 находится в одной плоскости с осью изделия.
1.2. На расстоянии h0, равном

от горизонтальной прямой, проведенной через точку О1 проводят параллельную ей прямую. На этой прямой расположится центр инструмента О0. Затем из точки T1 на этой прямой делают засечку радиусом R1. Таким образом определяют положение центра резца (точки О0 расчетной схемы).
1.3. Для удобства дальнейших вычислений обозначим расстояние по горизонтали между центром инструмента О0 и точками T1 и T2 обозначим символами E1 и E2, а расстояние между центрами детали и инструмента обозначим символом L.